A Detailed Look at the Manufacturing Processes of an Urn
In today’s world in which products are made increasingly by machine instead of by hand, a trend that will only become more common with the advent of technologies such as three dimensional printing, it comes as some relief to many that cremation urns are still often made by hand. While there are plenty of examples of popular, inexpensive urns being made by assembly line automation, the machinery used for urns keeps the automation to a minimum typically and, as we say, there are still plenty of cremation urns available that are made entirely by the hands of craftsmen and artists. (You can know that you are getting a hand-made urn when the picture you see on the online site from which you are working says something to the effect of , “This is a one of a kind item. Your product may vary slightly.” One of the draw backs to hand made cremation urns is that consumers cannot be assure an entirely uniform look of the finished product. This is the reason many manufacturers have learned that, perhaps, automated manufacturing – at least to some extend – is their best approach.)
Because of the interest in this topic, we have assembled this brief guide to how several of the best selling types of cremation urns are made.
Bronze Urns:
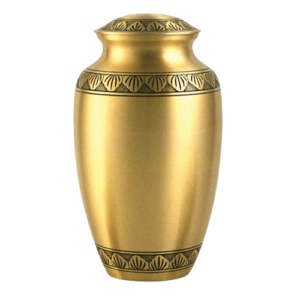
Bronze urns are classic urns and are solid. While other metal urns are typically shaped and produced by machine – with plenty of oversight from human eyes and hands to catch imperfections – bronze cremation urns are still commonly produced following age old manufacturing methods. The most common way to produce a bronze urn (or any bronze sculpture) is the “lost wax casting” method. In a nutshell, with the lost wax method, an artist makes a mold of the urn out of wax and then pours liquid bronze into the mold which can then be heated again (after the liquid has cooled) so that the wax mold will simply melt away from the finished urn. This process has been modernized by 20th (and 21st) century machinery that helps restore the mold so that an artist’s work is not lost after just one urn. And, while, even with these innovations, it is a significantly labor intensive production method for urns, but, since bronze is generally considered an expensive metal, manufacturers can add the above-average labor costs to the price of an urn, and consumers – already expecting to pay a high price for a bronze urn – won’t object. Hence, the centuries-old basic process remains practical even in the midst of modern technology that might make the process less labor intensive.
Cloisonne Urns:
Cloisonne urns, of all the urns whose manufacturing process we are describing today may be in the most danger of becoming obsolete. This ancient process of producing urns and many other types of ceramic art, does not have the benefit of an expensive material behind which labor costs can be hidden (as we saw above with bronze urns). In a nutshell, cloisonné urns are made by an artist who creates a wire shell (or skeleton) upon which a ceramic coating is placed and then heated in a kiln and decorated with paints and dies. The wire skeleton gives the urn stronger support than an urn made only from clay or some other ceramic material. These pieces can sometimes be repaired more easily than traditional clay, making them a secure home for cremation remains intended to be stored for many years. The problem manufacturers have with cloisonne urns is that automating the centuries old cloisonne process is complicated and impractical. (Attempts have reportedly been made, but most cloisonné urns sold today are all made by human hand, albeit, perhaps in an assembly line process involving several people for each urn produced.)
Wood Urns:
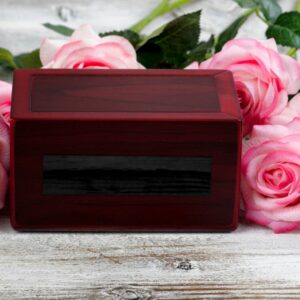
Wood urns are similarly produced in an assembly line process in most cases, though automated engraving and cutting machines make it more suitable for mass production than cloisonne. In a nutshell, an artist designs an create a single wood urn completely by hand, then machines can be set to create individual pieces of the urn in mass quantities. These pieces can then be set into still other machines that adhere the pieces together according to the original artists’ plan, or they can be hand glued in assembly line fashion by human hands. Either way, there is little threat of taking the human hand entirely out of the manufacturing process of wood urns. Even if machines are set to cut the pieces and then glue them together, a human will likely always be required to physically put the pieces into the machines that will do the work.
Other Metal Urns:
Metal urns made of materials besides bronze are typically manufactured via a spinning process in which sheets of metal are placed on fast moving spinning wheels and shaped into form, interestingly much as a pottery wheel does. This process is usually entirely mechanical, however, though it does require an artisan’s touch in the operation of the machinery that does the work. Steel and other similar metals do not work well for molded pieces such as bronze urns because their properties do not easily allow for a smooth transition between liquid and solid form. Metal urns, therefore, are usually single pieces of beautiful, smooth design that can sometimes be enhanced with the use of paint or finishes.
Glass Urns:
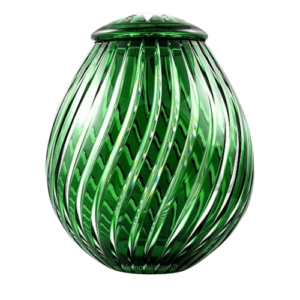
Glass urns are usually made by a blowing process that has been used for centuries to create all sorts of glass art that is surprisingly sturdy and long lasting. The chemical process by which glass cremation urns are created is sometimes considered a mystery even to the practitioners of glass art. So we will not attempt to describe it here. Suffice it to say that glass blowing is perhaps the only urn manufacturing method in common use today in which a bit of the actual cremation remains of a person who had died can be incorporated directly into the art itself. Many companies offer special services in which an urn can be ordered custom made after a cremation has taken place and a small amount of the ashes are mailed to the production company’s headquarters. The artist then carefully incorporates the ashes into the art as he or she is blowing the glass piece, and the final work is returned to the family, with the ashes clearly visible in the work itself. These glass pieces are sometimes made into full-fledge traditional urns that can hold all of the remaining ashes, but, in other cases, the rest of the ashes are either scattered or stored in a different container, and the glass piece becomes simply a work of art rather than a full cremation urn.
We hope that this article helps you appreciate the amount of work and care that goes in to the manufacturing of any cremation urn that you may consider buying to preserve your loved one’s memory. As we say, in this day in which automation is taking over just about every aspect of manufacturing it is refreshing for many people to know that at least one realm of manufacturing combines plenty of artistic skill with modern technology to help families keep their precious memories alive for the ages.